きさげ加工の基本工具『スクレーパー』を作る!10年使ってもヘタリにくい柄とは
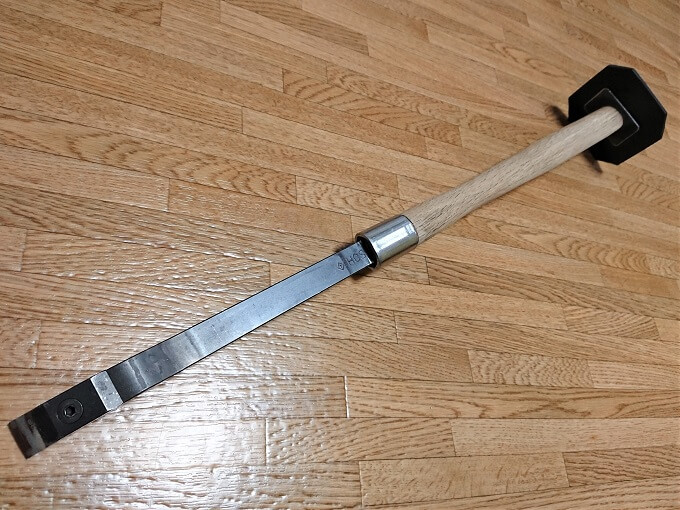
どうも!職人ライダーのヒロです。
今日は きさげ加工の基本工具
“スクレーパー”の作り方をご紹介します!
※今回ご紹介するのは腰きさげ用になります。
この方法で作ったスクレーパーを
10年間以上毎日使用してますが、
全くヘタるということがありません。
このページでは経年劣化によってガタついてくる
という意味で使用します。
きさげ加工では、スクレーパーにかなりの負荷をかけて金属を削ります。
そのため長年使っていると、柄と金属の接合部分(下の写真)が
経年劣化によりガタつくことがあります ⇩
ここにウエス等をかませて使っている人をよく目にしますが
少しでもガタツキがあると、
負荷をかけるたびにガタツキがどんどん大きくなり
最終的には使い物にならなくなります。
- これからスクレーパーを作りたい方
- 柄がガタガタなので作り直したい方
今回ご紹介する方法でスクレーパーを作ってみて下さい。
きっと耐久性の良いものが作れると思います!
ちなみに、
いま使っているスクレーパーを修理して使いたい!
という方もいるでしょう。
ガタツキ度合いが軽度の物なら修理できる可能性があります。
柄の修理方法を掲載した記事もあるので
修理してみたい方は
こちらの記事がおすすめです ⇩
この方法で修理した柄はかなり頑丈になるので、
補強したいという方にもおすすめです。
きさげ加工とはどういった加工なのか?
これから きさげ を覚えるけどあまり良く知らないという方は
こちらの記事をどうぞ⇩
目次
きさげ加工の基本工具 ヘタリにくいスクレーパーの柄とは
なぜヘタリにくいスクレーパーが作れるのか?
まずはネタばらしからお話しします。
急所となる部分は二つあって
まず一つ目に
スクレーパーの金属部分(柄との接合部分)を
くさび形 にしてしまうということ。
テーパー形状のくさび形にする事で、どんどん柄に食いついて密着する。
しっかり密着する事によって、どんなに負荷をかけてもガタツキが起こらないのです。
二つ目は
スクレーパーと柄の接合部分に使っているカラーを
大小サイズの違うもの2つ用意します。
- 内径大きめのカラー
- 内径小さめのカラー
上記2つ用意する
それを作成手順の進みぐあいによって交換することによって
より強固に締めつけられる。
柄からスクレーパーを抜く方が難しくなるくらい丈夫な物が作れます。
やり方はのちに説明するので
まずここでは
- スクレーパーをくさび形に加工する
- 作成の進みぐあいによってサイズの小さいカラーに交換する
ざっくり上記のことを
頭に入れておいてもらえてば良いと思います。
きさげ工具 スクレーパー を作成する
今回は私が使っているスクレーパーを基準にしてご紹介します。
きさげ加工を施すところや使い勝手によって
スクレーパーの長さも変わりますが
作成方法としては同じなので
参考にして頂ければと思います。
材料として使用する部品
使用する材料として絶対必要なのがこの3点。
- 柄の素材
- カラー2つ(大小サイズの違うもの)
- クランプ式スクレーパー
柄の材料として ⇩
オーエッチ工業さんの商品を使用しました。
元々は両口ハンマー用の柄で3.6㎏~13.5㎏まで使用できる物。
スクレーパー用としては
重さも耐久性も申し分のない代物です!
柄とスクレーパーの接合部分に打ち込む金属カラー ⇩
カラーは焼きばめ時(後工程で説明)に使用する大きいサイズと
最終的に使用する小さいサイズの物
二つ用意します。
ワンサイズ大きめのカラー⇩
焼きばめ時に 柄の割れを防止するため 仮に打ち込むカラーです。
最終的に使用する物よりワンサイズ大き目の物を用意します。
今回は銅管ソケット(内径25.4㎜)を使用。
ワンサイズ小さめのカラー⇩
最終的に打ち込むワンサイズ小さめのカラー
耐久性の良いガス管がおすすめ。
今回はガス管3/4サイズ(内径21.5mm)を使用。
最終的に使用するカラーは耐久性の良い物がおすすめ!
耐久性の弱いカラーを使用すると強度が維持できず
柄が割れてくる現象が生じます。
ある程度の粘り強さと強度を兼ね備えた物を使用して下さい。
クランプ式スクレーパー⇩
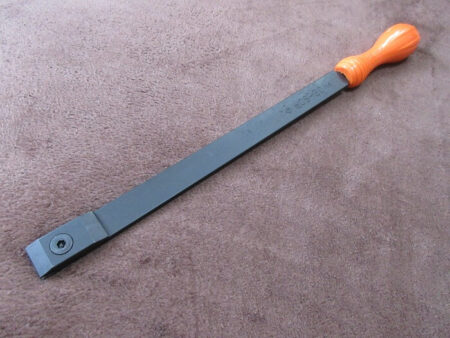
タンガロイさんの商品を使用
クランプ式スクレーパーだと チップを研いで4面つかえるし
チップが減っても交換すればいいので超便利!
柄に大きめのカラー(仮のもの)を打ち込む
焼きばめ時に使用するだけの仮カラーです。
もしカラーなしで焼きばめすると
柄が割れてしまうため必要な工程です。
まずはカラーをバイスや万力でつかんで、ダエン形にして平べったくします⇩
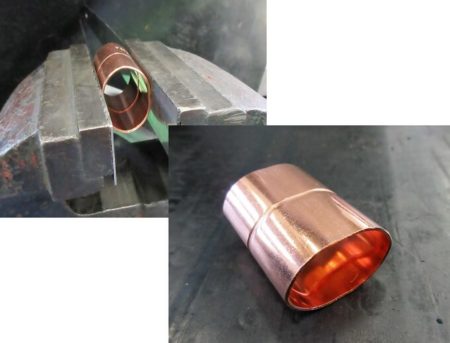
※スクレーバー本体を打ち込む事を考慮した大きさにする。
平べったくしたカラーを柄の方へ打ち込みましょう。
そのままでは入らないので、
カラーの形状に合うように柄を削っていきます⇩
カラーと柄のクリアランスは、ユルユルにせず
叩き込んで無理やりはめ込む感じにすること!
ユルユルだと使い物になりません。
カラーが入りそうな形状になってきたら
樹脂ハンマーで叩いて無理やりはめ込んでいく⇩
どうしても入らなかったら柄を削りながら更に叩き込む⇩
- 樹脂ハンマーで叩き込む
- そのまま柄を削る
- 樹脂ハンマーで叩き込む
この作業を繰り返してカラーを無理やり打ち込んでください。
ガスであぶってスクレーパーをまげる
曲げないで使うスクレーパーもありますが
クランプ式スクレーパーは曲げないと使いにくいので
下の写真を参考にし
ガスであぶって曲げてください。
寸法は上の写真を参考にしていただいて
曲げる角度についは人によって力のかけ具合やクセも違うと思います。
まずは上の写真を参考にしていただいて
実際つかってみて自分に合う角度をさがしてみてください。
曲げる時は必ずガスであぶって曲げましょう。
バイス等で挟んで無理やり曲げたり
ベンダーで曲げるとこうなります⇩
曲げる時はガスであぶって曲げましょう。
スクレーパーをくさび形に加工する
スクレーパーの柄との接合部分を くさび形 に加工しましょう。
まずは加工するラインをケガキます⇩
スクレーパーに対して4面共くさび形に加工します。
加工ライン、センターライン共に
きっちりケガキましょう。
ケガキ線にそってサンダー(ディスクグラインダー)で加工⇩
スクレーパー中心に対してセンター出し必須のこと!
出来るだけキレイに加工しましょう。
くさび形に加工したスクレーパー⇩
スクレーパー中心に対して 4面のセンター出しをきっちりすること!
これがズレると焼きばめ時に ずれて柄が使いものになりません
くさびの4面はキッチリセンター出ししてください。
ガイド用の穴をあける
スクレーパー本体の厚みと同径の穴を柄のセンターにあける。
その両サイドにもガイド用の穴をあける。
穴の長さは柄に差しこむスクレーパーの長さ寸法。
※上の写真参照
特に中央の穴だけは
センターど真ん中にきっちり開ける事!
ズレていると焼いて柄にはめていく時にズレル可能性あり!
センターだけは正確にお願いします。
ガスであぶって焼きばめする
この工程では
先ほどスクレーパーのくさび形に加工した部分をガスであぶり
柄を焼きばめする。
そういう工程になります!
今回の作業で一番重要な工程なので慎重におこなってください。
失敗すると1からやり直しとなります。
ガスを使用するなどの 危険も伴います。
ガスであぶる人/柄を差し込む人に分かれて、
必ず二人作業でおこないましょう!
まずは くさび形に加工したスクレーパーを
バイス台に固定して出来るだけまっすぐにしましょう。
そしてガスであぶる ⇩
くさび部が赤くなるまであぶってください。
※やり過ぎると溶けるので注意!
間髪入れずに柄を差し込んでください⇩
※出来るだけまっすぐに!
歪んで入ると使いものにならないので
真っすぐかどうかヨコで誰かに見てもらって
必ず二人作業でおこなってください。
「入らなくなった」と感じたら直ぐに抜いて
もう一度ガスであぶって入れる。
予定の位置まで追い込んでください。
最後まで差し込んだら直ぐに柄を抜くこと!
差したままにしていると熱で穴が広がり
使い物にならなくなります。
焼きばめした後の柄をそのままにしておくと
発火する恐れがあるので 水で濡らせておきましょう。
くさび形に加工したスクレーパーの先は
尖っていて危ないので軽く面取しておきましょう。
スクレーパーを柄に打ち込んでカラーを交換する
柄がかわいたらスクレーパーを柄に打ち込んでください。
そして仮に打ち込んでいたカラーを抜きましょう。
マイナスドライバーやキー材など
何か平たいものを利用して抜いてください。
そして仮に打ち込んでいたカラーより
ワンサイス小さめのカラーを打ち込んでいきましょう。
カラーを打ち込む手順は最初に説明した通り
すこしづつ削りながらかなりキツめに打ち込む感じ。
キー材などの長い棒を利用してガンガン叩いて打ち込んでください。
必ずスクレーパーを柄に打ち込んだ状態で作業すること!
スクレーパーを打ち込まずに作業すると
穴が割れてしまいます。
ガンガン叩いているとスクレーパーが抜けてきます。
気をつけながらスクレーパーを再度打ち込んで
スクレーパーが抜けた状態にならないこと!
キー材とかで叩いていると下の写真の様になるので
サンダーやヤスリを使って形を整えてください。
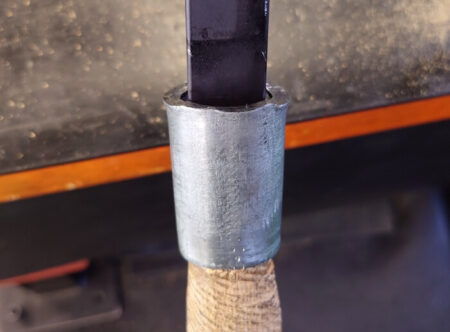
カラーボコボコ
その際も必ずスクレーパーを柄に打ち込んだ状態で作業すること!
柄の形を整える
柄を削ってくびれをつけましょう。
くびれをつける理由はシナリを良くするめです。
なにもせずに使うとかなり堅いキサゲになります。
その他の部分も削ってキレイに形を整えましょう。
そして自分の使いやすい長さにカットする。
短すぎるとどうにもならないので
少し長めにカットすると後で調整がしやすいです。
ちなみに身長162㎝の私が使っているスクレーパー寸法は以下のとおり⇩
どうぞご参考までに。
身体に当てる部分にクッションを取り付ける
柄のお尻(身体に当てる部分)にはクッションを付けましょう。
クッション素材はハッキリ言って何でも良いです。
ちなみに私はこんな感じにしています ⇩
厚み4㎜ほどの鉄板で設置面積を大きくし
厚み5㎜のゴム板をかませて使ってます。
これでけっこう楽に使えてます!
そして完成!
良いスクレーパーは作れましたか?
お疲れ様でした。
最後に
今回ご紹介したスクレーパー作成方法は、
今は定年退職された会社の大先輩の方
私が尊敬する大先輩から教えて頂いたノウハウです。
それを元に更に強固になるよう改良を加えてお伝えさせて頂きました。
その方のお言葉。
「お前に作り方教えたるけど、お前はまたみんなに教えたれよ!」
その言葉の通りこの方法を記事にすることにしました。
この方法でスクレーパーを作成すると
10年以上毎日使ってもヘタレる事のない
すごく耐久性の良いスクレーパーが作れます!
10年以上 毎日体重をかけ続け、めちゃくちゃ負荷がかかっているにも関わらず
びくともしない!
めちゃくちゃ頑丈なスクレーパーです!
今回この記事を作成するにあたり、久しぶりにもう一本作ってみました。
ちなみにスクレーパーだけでなく、
“ささばきさげ”に使う ささっぱの柄 もこの方法で作成できます。
作り方の原理は同じです。
ささっぱ は柄との接合部分にさほど負荷もかからないので
今回ご紹介したようにカラーを入れ替える必要はありません。
なのでもっと楽に作れます。
これから きさげ を学ぶ職人見習いの方。
スクレーパーのガタツキにお悩みの方。
是非この方法でスクレーパーを作ってみて下さい!
今回は以上です。
この記事がお役に立てれば幸いです。
必ず自己責任でお願いします。
万が一事故が起こった場合でも、当方では責任を負えませんのでご注意下さい。
Comment
はじめまして
石川県金沢市の岡崎豊徳と申します
柄付きキサゲが欲しいです
私の為に一本作っていただけないでしょうか?
お金で買える物ではないと思ってますが謝礼は致します
初めまして。
当方。工業高校の教員をしております。
数か月の練習であたりを出せるほどのキサゲをかけれるとは思っておりませんが、生徒にキサゲ加工を見せたいと思っております。
そこで移動先の高校で先輩先生が残していったキサゲの刃物を復活させたいとおもっております。
地元企業の見学に伺った際、ダイヤモンドホイールの両頭グラインダで刃先を仕上げているのを拝見しました。
一方で包丁を砥ぐような四角い砥石で刃先を仕上げているのも他所の工場で拝見しました。。
職人ライダーヒロさんの工場では、どのような手段で刃先を仕上げておいでですか。
もし、可能であれば砥石の番手など教えていただけると助かります。
初めまして!
コメントありがとうございます。
弊社の工場では超硬チップしか使用しないので
ダイヤモンド砥石を使用して刃物を研いでいます。
使用している砥石は岡崎精工さんの物で
U.S WHEEL ダイヤモンド
1520 SDC220-N100BD 45-2.0
上記の物を使用しています。
どうかご参考までに。
はじめまして。
きさげを学んでおり、工作機械の組み立てをしている企業の方々と議論をしております。
やはり問題になるのは「あたりの評価方法」です。お客様との意見が食い違う場面もあるようです。
どのようは評価をしていらっしゃるのでしょうか?
坪当たりであれば、なんとなく理解できますが、パーセント当たりだとすると…?
マル秘の部分もお有りでしょうから、ヒントでも構いません。
黒当たりの様子が写真で見ることができれば…(これがマル秘ですよね)。
私は長野県在住です。バイクでお越しの際、お目にかかれると嬉しいです。
要求ばかりですみません。
ご助言いただけると幸いです。